Direct Pipe
The Game-Changing Approach to Pipeline Installation
Direct Pipe® technology is a breakthrough in the field of pipeline installation that ingeniously combines the strengths of microtunnelling and horizontal directional drilling technology (HDD).
This one-step technology operates in a multitude of geological terrains from soft to heterogeneous soils, and even solid rock, and is designed to handle pipe diameters ranging between 0.8 and 1.5m (30-60").
In an efficient and economical manner, this innovation enables the simultaneous installation of a prefabricated pipeline and creation of the required borehole. This method permits the rapid and cost-effective laying of pipelines exceeding 1,500 meters in length.
Seamlessly Integrating Two Technologies for Enhanced Performance
Direct Pipe® technology integrates two technologies in a seamless manner:
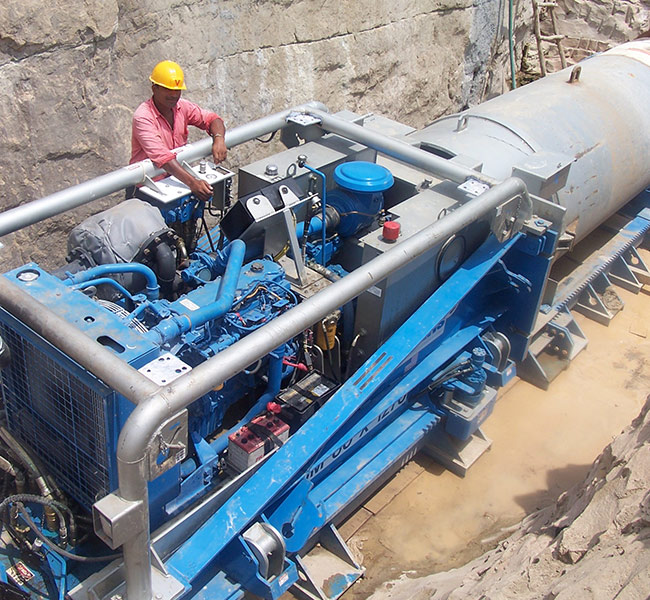
Soil Excavation
The process begins with the removal of soil from the starting pit utilizing a liquid-supported microtunnelling machine. This machine effectively transports the overburden via a conveyor circuit within the prefabricated pipeline above ground, directing it to a separation plant.
Pipeline Installation
Concurrently with the drilling, the pipeline, which is assembled above ground on roller blocks and welded to the machine, is impelled into the drilled hole. A pipe thruster delivers the required propulsion force, pushing the microtunnelling machine along with the pipeline with a thrust of up to 750 tons in strokes of 5 meters.
The working face can be monitored consistently and reliably, even in diverse, water-permeable soils. Uphill and downhill gradients, as well as precise cornering during the route, are feasible, thanks to a gyro-based navigation system.
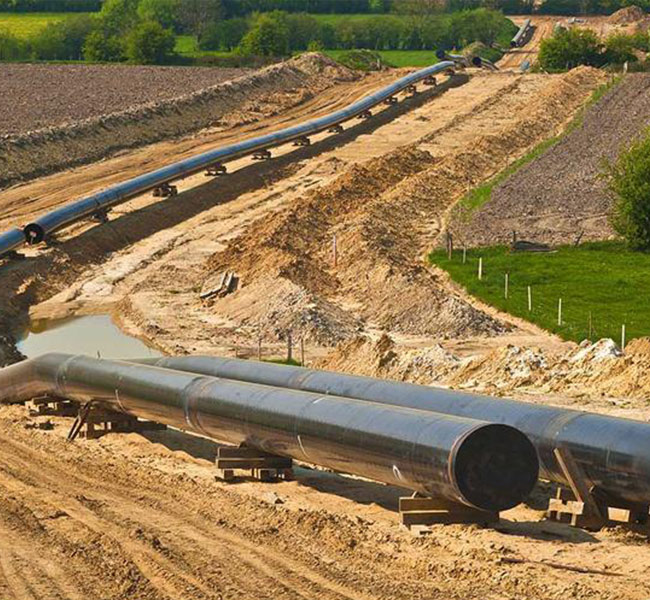
An Overview of the Working Mechanism of Direct Pipe
Direct Pipe® system operates in a logical, methodical sequence:
Soil is excavated by the AVN machine’s specialized tools.
The front of the excavation is supported hydraulically via liquid suspension.
The overburden is moved through a hydraulic pumping circuit via lines laid within the pipeline.
The Pipe Thruster pushes the AVN machine along the pipeline.
Finally, the pipeline is installed in the tunnel created.